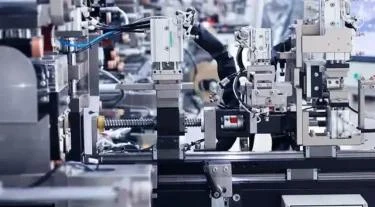
# Tape Manufacturing Process and Techniques
## Introduction to Tape Manufacturing
Tape manufacturing is a complex process that involves multiple stages to produce various types of adhesive tapes for different applications. From everyday household tapes to specialized industrial tapes, the manufacturing process requires precision and careful quality control.
## Raw Materials Used in Tape Production
The primary components of most tapes include:
– Backing material (plastic films, paper, cloth, or foil)
– Adhesive (rubber-based, acrylic, or silicone)
– Release liner (for some tape types)
– Additives (tackifiers, stabilizers, and other chemicals)
## The Tape Manufacturing Process
### 1. Backing Material Preparation
The process begins with preparing the backing material:
– Plastic films are extruded or cast
– Paper backings are treated for strength and moisture resistance
– Fabric backings are woven and coated
### 2. Adhesive Application
There are several methods for applying adhesive:
#### Solution Coating
The adhesive is dissolved in a solvent and applied to the backing material. The solvent is then evaporated in drying ovens.
#### Hot Melt Coating
The adhesive is heated to a liquid state and applied directly to the backing material without solvents.
#### Water-Based Coating
Similar to solution coating but uses water as the carrier instead of organic solvents.
### 3. Drying and Curing
After application, the adhesive must be properly dried or cured:
– Solvent-based adhesives require extensive drying to remove all solvents
– Hot melt adhesives cool and solidify quickly
– Some adhesives require UV or thermal curing
### 4. Lamination (if applicable)
For tapes with multiple layers or special properties:
– Additional layers may be laminated to the adhesive-coated backing
– Release liners are applied for pressure-sensitive tapes
### 5. Slitting and Rewinding
The large rolls of coated material are slit into narrower widths:
– Precision slitting machines cut the material to specified widths
– The tape is rewound onto cores for packaging
### 6. Quality Control and Testing
Throughout the process, quality checks ensure:
– Proper adhesive thickness and uniformity
– Correct tape width and length
– Adhesive performance (tack, peel strength, shear resistance)
– Backing material integrity
## Specialized Tape Manufacturing Techniques
### Double-Sided Tape Production
Involves applying adhesive to both sides of a carrier material with a release liner in between.
### Foam Tape Manufacturing
Uses special foam backings that are coated with adhesive for vibration damping and gap filling applications.
### Electrical Tape Production
Requires materials with specific dielectric properties and often involves special curing processes.
## Environmental Considerations
Modern tape manufacturing focuses on:
– Reducing solvent use and VOC emissions
– Developing water-based and solvent-free adhesives
– Implementing recycling programs for production waste
– Using sustainable raw materials where possible
## Future Trends in Tape Manufacturing
Emerging technologies include:
– Nanotechnology-enhanced adhesives
– Biodegradable tape materials
– Smart tapes with embedded sensors
– More efficient production methods
The tape manufacturing industry continues to evolve, developing new products and processes to meet changing market demands while addressing environmental concerns.
Keyword: tape manufacturing